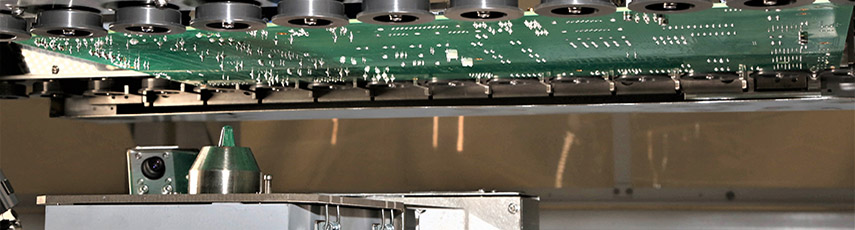
Pillarhouse International
About the industry partner
Founded in 1978, Pillarhouse International pioneered the design and manufacture of specialist equipment for the coil winding and associated industries.
The company produced its first production soldering system in 1984, and with continued growth throughout the 1980’s, used this technology to develop the world’s first selective soldering machine in 1994.
Pillarhouse International continues to be a world leader in the selective soldering industry, dedicated to the ongoing development of pioneering technologies to reflect and match the needs of an everchanging manufacturing marketplace. They offer a wide range of selective soldering machines, covering the complexity of global demand for production across electronics, aerospace and PCB contract manufacturing.
The Challenge
Selective soldering utilises wettable metal nozzles for controlled application of solder to plated through hole components. Nozzles can last for hundreds of hours with the correct maintenance, however de-wetting and eventual wear results in a machine downtime, loss of productivity revenue and an increase in product rework. Performance improvements to selective soldering nozzles allows for operation in more demanding process environments, producing higher quality and more reliable products whilst also reducing process downtime and producing fewer defects.
A joint research project between industry and academia was established in January 2021 to investigate the fundamental wear mechanisms of selective soldering nozzles and develop improved nozzles, from alternative alloys, with increased wettability and lifetime.
The Solution
Pillarhouse International worked collaboratively with Coventry University experts to support the research journey of a Knowledge Transfer Partnership (KTP) associate to develop a new nozzle. By combining the studies of materials science, tribology (study of interacting surface and wear) and surface engineering, they were able to analyse both the wear characteristics and wetting of different materials to choose the best options. Following this, surface treatments and coatings were applied to modify the materials’ characteristics and further enhance performance.
Prototype testing was undertaken with certain customers to generate field data and land upon a final design that is now being taken to manufacture.
The design has over 8 times the lifetime of the company's current nozzles and with over twice the wettability. The new AP Master Nozzle will be available for purchase from June 2023.