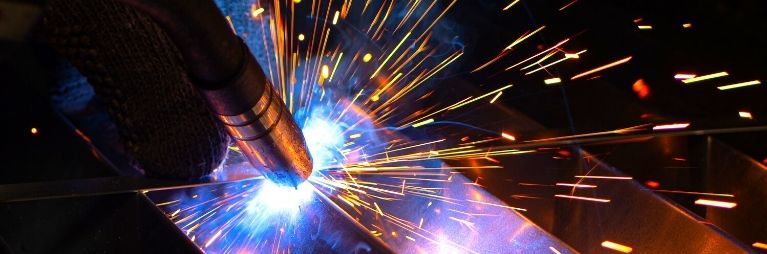
Structural Integrity and Non-Destructive Testing
Focus of our research
Our research focuses on the development and application of materials and methods that find use in safety-critical applications, and the fundamental scientific knowledge required to assure and improve safety.
We work on novel design concepts, characterization of materials properties, development of novel analytical and processing techniques and fundamental mechanistic understanding for improvement in product lifetime. By understanding in-service material behaviour, we support our industrial partners in producing superior and more cost-effective products with longer lifespans.
Our current research includes:
- Study of the performance of materials for aerospace and energy applications, especially novel materials made by advanced manufacturing processes
- Development and application of novel surface engineering treatments such as laser shock peening to make materials more durable in service
- Development and application of advanced instrumentation for materials characterization, including neutron and synchrotron X-ray techniques
- Non-destructive evaluation using evolutionary computing techniques
- Residual stress analysis and stress engineering
- Atomic scale modelling of energy materials.
- Micro and Nano mechanical testing (AFM, Nano-Indentation, and in situ SEM)
If you wish to find out more about this theme, please get in contact with Professor Michael Fitzpatrick and Professor Xiang Zhang.
Key researchers
Name | Title | |
---|---|---|
Professor Xiang Zhang | Theme lead. Professor of Structural Integrity | ab8295@coventry.ac.uk |
Dr James Griffin | Associate Professor | ac0393@coventry.ac.uk |
Dr M Kashif Khan | Assistant Professor | ac1291@coventry.ac.uk |
Dr Abdul Khadar Syed | Assistant Professor | ab9237@coventry.ac.uk |
Zhaohe Gao | Assistant Professor | ae2818@coventry.ac.uk |
Dr Ping Lu | Assistant Professor | ad9918@coventry.ac.uk |
Dr Bilal Ahmed | Research Fellow | ac2333@coventry.ac.uk |
Dr Niall Smyth | Research Fellow | ab7883@coventry.ac.uk |
Jiangjing Xi | Research Fellow | ae2923@coventry.ac.uk |
Projects
Our research aims to increase our fundamental mechanistic understanding of material response, through characterization of materials properties, and development of novel analytical and processing techniques, to provide design solutions for the benefit of human and product safety. Find out more about some of our projects:
NEWAM. EPSRC Programme Grant “New Wire Additive Manufacturing (NEWAM)” aims for large-area additive manufacturing of new generation metallic alloys for the aerospace and energy industries, through process innovation and material science and engineering. Coventry University leads the Material Performance theme investigating the durability and damage tolerance performance via material characterisation, testing, and modelling and simulation.
NOMAD EU H2020. “Non-destructive Evaluation (NDE) System for the Inspection of Operation-Induced Material Degradation in Nuclear Power Plants (NPPs)” looks at combining a range of non-destructive testing capabilities for the detection of embrittlement during the exposure of irradiation.
This work is specifically focused towards Reactor Pressure Vessels (RPVs Type II and III) to ensure less conservative and more dynamic and accurate measurements are made in terms of safety-critical structure extension to life.
Coventry’s participation looks into the use of Barkhausen Noise coupled with Acoustic Emission to detect embrittlement.
Laser Shock Peening (funded by Airbus). Laser peening allows for the precise placement of highly compressive residual stresses in a component and has been used to modify the trajectory of fatigue cracks.
The change in crack path is achieved by placing rotated residual stress fields in the proximity of the propagating crack. This exposes the crack to a unique loading configuration and results in the crack deviation.
Experimental and simulation methods have been used to characterise the influence of the residual stresses on the trajectory of fatigue cracks. This ideally can be used to reduce the weight of aircraft structures whilst maintaining the highest level of safety.
Harvestore EU H2020. This involves the production of new artificial materials with superior performance. Fast electrical conduction and high charge storage capacity will be achieved by taking advantage of nanoscale engineering.
The project further integrates the use of silicon technology, combining unique properties of manufacturability, abundance and low environmental impact.