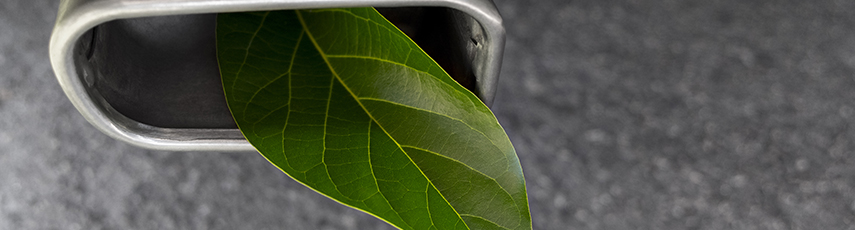
InnEx
Funder
Innovate UK
Total value of project
£973,823
Value to Coventry University
£229,027
Project team
Dr Christophe Bastien, Dr Jesper Christensen
Collaborators
Unipart Powertrain Applications Ltd (Lead); Jaguar Land Rover Ltd, Coventry; Ricor Limited, Studley; Johnson Matthey, London; TWI The Welding Institute
Duration of project
01/07/2015 - 30/06/2017
Project overview
The project will develop a new highly innovative lightweight exhaust system for forced induction diesel and petrol automotive vehicles.
This project will deliver cost-effective materials and manufacturing technology, including metrology and CAE methods to enable a step change reduction of 50% of the mass of an exhaust system. It will provide innovative solutions to the manufacturing challenges associated with down-gauging exhaust components in terms of jigging, forming, joining and metrology as well as the overall design methodology.
The project will also focus on the development of new and innovative material processes for the hot-end of the exhaust system including the associated manufacturing challenges. The ultimate aim is to significantly reduce the overall system mass, thus for instance giving an annual CO2 saving of 325m tonnes for cars, fuel savings and a significant reduction of precious metals being used in catalytic converters. The project brings together 5 organisations in a 2 year project.
Project objectives
The Ultra Lightweight Exhaust project aligns with the scope of the competition by aiming to achieve lightweight vehicle and powertrain structures. The major objectives are:
- Cost-effective material/manufacturing technologies that will deliver a step change in weight reduction for a given system or product requirement. This outcome will be obtained by the use of cost-effective materials and manufacturing technology, including metrology and CAE methods.
- Designs and production processes that enable substitution or reduction of lightweight materials which are scarce, harmful or difficult to recycle will be achieved by reducing the amount of precious metals required in a comparable exhaust system. This outcome will be obtained due to the fact that a lighter/thinner gauge system with less thermal mass/inertia will reach its operating temperature more quickly requiring less precious metal in its catalytic converter.
The project has considerable but measured technical risk and requires a highly skilled multi-disciplinary team to work in close collaboration to develop and exploit the outputs.