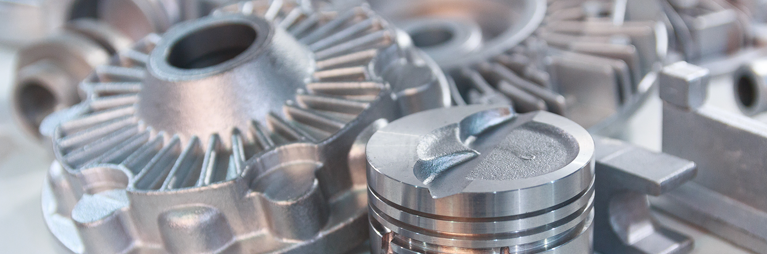
3D Printed Cooling channels for extended tooling life
Funder
Innovate UK
Value
£235,573
Team
Dr Essam Abdelfatah (PI), Dr James Jewkes, Mr Tonyan Zeng, Mr Yuancheng Liang
Duration
1 April 2018 to 31 February 2021
Project objectives
The objective of the project is to develop a full thermal and optimization model to design cooling channels in a direct metal laser sintering (DMLS) steel tool for high pressure aluminium die-casting (HPADC). The aim is to enhance the design of the printed tool component, using Renishaw’s 3D printing technology, to increase the potential number of units that can be cast at CastAlum to a possible 150,000 units for the same mould. At the same time the intention is to ensure that CastAlum’s printed and optimally cooled tool can maintain the quality and compliance of the cast parts within the critical specifications of their automotive manufacturers’ supply chain.
Optimising the direct metal laser sintering process makes the manufacture of accurate, pressure tight components possible. The design rules and methodology for the conformal cooling channels to cool the tool uniformly during the casting operation will be developed through computational fluid dynamic (CFD) simulation and optimization techniques. The CFD model developed by Coventry University will then be combined with a finite element (FE) model for the design and manufacture of the high pressure aluminium die-casting tool or inserts using fully computer aided design/computer aided manufacture (CAD/CAM) processes.
Initial trials with comparative tooling will be undertaken to provide evidence for the business case for investment in the technology. The development of the cooling control system, and the optimised tool surface finish, will lead to improved quality and reduced costs through a reduction in reject rate and significant tool life improvement.
The Fluid and Complex System Research Centre's (FCS) contributions to the work are:
- Objective 1: Parametric simulation of an existing non-conformal channel mold
- Objective 2: Experimental data collection for the validation of the simulation model
- Objective 2: Simulation of conformal channels for various inserts and a full tool
- Objective 3: Development of a methodology for designing conformal cooling channels to achieve an effective and uniform cooling for the cast parts.
- Objective 4: Development of an adjoint optimization method to alter the cooling channel geometry in order to achieve a uniform cooling regime.
Impact
Three groups of beneficiaries have been classed according to the immediacy of the benefits received as a result of the project.
Immediate to short-term benefits (< 5 years):
Researchers involved in the project and engineering undergraduate and postgraduate students associated with the Fluid and Complex Systems Centre.
The most immediate beneficiaries of the proposed project have been identified as the researchers directly involved in the work. The postdoctoral research assistant (PDRA) will be able to take advantage of career development opportunities at Coventry University, while working on a cutting edge research project. They will become competent in modelling techniques as well as the development of experimental techniques and sensor technologies for the model validation tasks, thus improving significantly their employability at the end of their appointment. In addition, the PDRA will develop new skills both in terms of research and personal development.
All researchers, namely the PI, Co-I and PDRA and the MRes student will participate in international conferences and attend training workshops not only with relevance to their research, but also as part of their personal development.
The collaborative proposal is a means of promoting FCS’s capabilities to a wider group of industrial beneficiaries as well as provide its members with industrial relevance and identify challenges for future research and development. The work also provides the opportunity of developing publications for journals and conferences as well as materials for manufacturing industry exhibitions, the Innovate-UK supported Knowledge Transfer Networks (KTN) and the Additive Manufacturing (AM) Catapult.
In addition, Undergraduate, Masters, Postgraduate and Engineering Doctorate students associated with the Centre will benefit from this work with a number conducting their research project in areas relevant to this project under the supervision of the PI and Co-I, and gaining practical experience of an industrially relevant challenge. These students will be exposed to the working ethos of commercially relevant research and development and will gain valuable experience for their future career. The findings from this work will be incorporated into teaching, where relevant.
The industrial partners. The immediate impact of the work is the identification of an optimal conformal cooling channel design for a specific piece being cast. The impact is expected to be a reduction in the cost and time to produce a casting tool, this being undertaken by Renishaw plc, and a consequent reduction in the cost (Capex) to the lead partner, CastAlum, through a longer tool life, hence a reduction in the cost of each item cast and an assurance of cast item quality (Opex) and subsequent lower rejection rates by their customers throughout the tool life.
Benefits for >5 year period:
For the >5 year period after the completion of the project the potential beneficiaries have been identified as the Advanced Manufacturing industry in the UK. AM has been identified as being one of the key enabling technologies for the development of high value manufacturing in the UK. In 2015, the industry was valued at $5.9 billion with 93% of this attributed to industrial applications. Previous applications of the technology have been limited to rapid prototyping, however, with advances in the technology, the uptake of AM in industries such as aerospace, automotive and medical has seen a significant increase. Once validated, rapid prototyping-assisted conformal cooling mold channelling will easily transfer from simulation into actual fabrication. For FCS the impact will be its increased competencies in addressing industrially relevant challenges and the further development and commercial exploitation of its high temperature materials’ modelling capabilities.
Long term (>10 years) benefits:
The UK economy will benefit as the conformal cooling aspect has applications in other industries, such as developing battery cooling enclosures for electric vehicles.
Outputs
The intended outputs are:
- Identification of the cooling layout and channel shape and size
- Determination of the limitations on additive manufactured tool strength and longevity of using a conformal cooling channel
- Identification of the spatial distribution of the temperature and uniformity index in the casting tool
- Identification of the cooling flow rate for serial and/or parallel coolant channels and the associated pressure drop and coolant temperature change
- Assessment of the influence of coolant flow conditions (laminar/turbulent) and influence of the cooling channel surface on the heat transfer characteristics and pressure drop
- Prediction of the heat transfer rate and therefore an estimation of cast cycle time
- Completion of the necessary modifications in the model to match the experimental data and assurance that the developed model can be used for designing other tools
The "safe” distances from the cooling media to any cast surface will also be determined based on the heat transfer rate and temperature gradient of the cast item/tool that will be carried out using FE analysis. An iterative design exercise will be carried out to achieve the optimum tool cooling design.